
Visit Okayama-pert 1
両ブランドを手掛けるのが、岡山県倉敷市児島に本社を構える(株)ドミンゴ。デニム製品のみならず、シャツやアウターなども手掛け、製品すべてがメイド・イン・ジャパンであることにこだわっています。
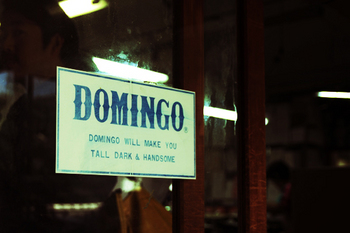
ドミンゴさんの製品を生み出している岡山県倉敷市児島の歴史背景には、古くは製塩業が。それから織物業、縫製業へと移り変わり、今現在でも学生服、作業着、デニムといった繊維産業が盛んで、日本製デニムの発祥の地として知られています。
そのドミンゴさんの生産背景を知り、より深い商品知識を得るべくドミンゴさんご協力の元、岡山を訪ねてきました。
1回目の本日は、「縫製」にスポットをあてたリポートをお届けします。
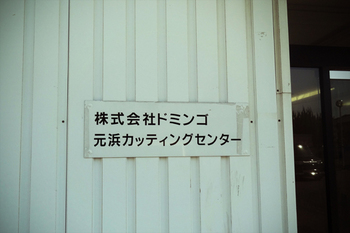
児島到着後、まず訪れたのが自社工場の元浜カッティングセンター。
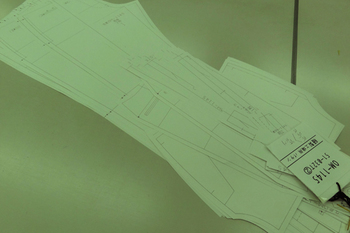
デザイン、企画を経てCADシステムで作製されたパターンをCAMというシステムで処理をしていきます。
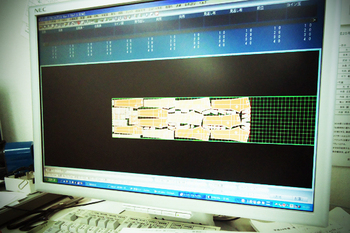
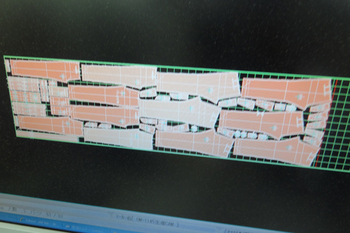
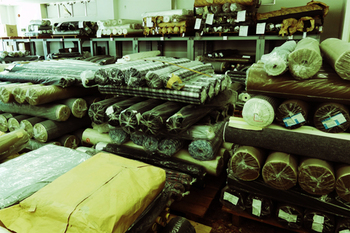
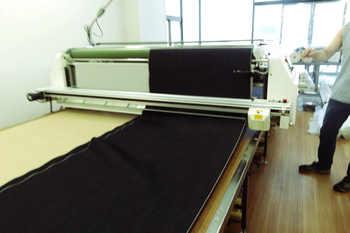
こちらは延反機。幾重にも重ねられた生地を正確に裁断していく為に必要な工程で、生地をまっすぐにし、裁断時に生地ごとの寸法にズレがないようにしていきます。
生地を置く台の下には、"エアスルー"と呼ばれる生地を下から圧縮する機会が設置されており、圧縮することで、厚みが減り、ズレが少なくなり一度に裁断できる量を増やしているそうです。
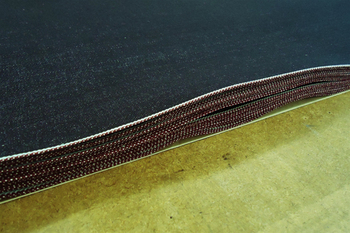
ただし、ここまで機械の力を借りていてもどうしても生じてしまうズレは、熟練の職人さんの"手"の感覚で微調整が行われるようです。
こうしてカッティングが終わり、次の工程が「縫製」。本社児島から、瀬戸大橋を渡って香川県さぬき市にある縫製工場に向かいます。
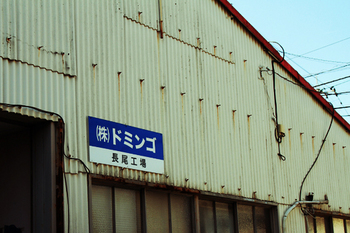
ドミンゴさん直営工場「長尾工場」。歴史を感じさせる街並みの中に現れた、ノスタルジックな雰囲気です。主にボトムスを中心とした縫製を行っています。
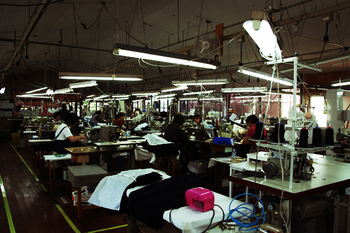
様々な工程にわかれ、順序よく作業が行われています。
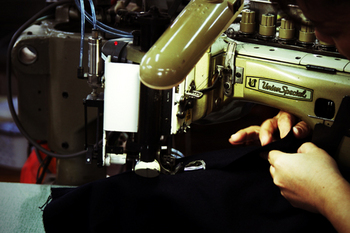
旧式の巻縫い専用ミシンを使用している様子。ジーンズの尻ぐりやパンツの脇などチェーンステッチで互いの生地を巻き込むように縫っています。
ガイドとなるような印はなく、ラッパと呼ばれる金具に巻き込んでいく加減は、職人さんの手によるところが大きく、熟練したレベルが必要なのだそう。
一般的なミシンしか目の当たりにしたことがない私は、素早く正確に仕上げていく、指先の一つ一つの動きに見入ってしまいました。
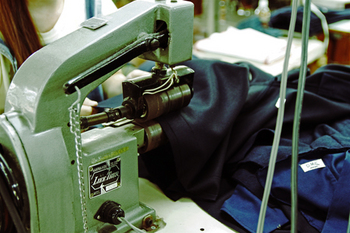
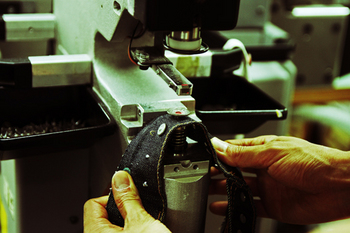
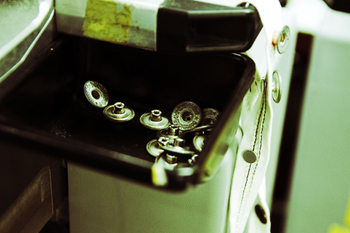
長尾工場の次は「津田工場」へ。
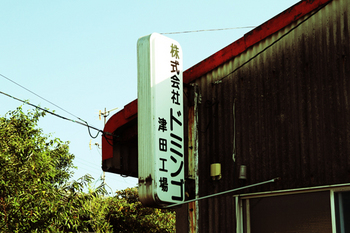
こちらではシャツの縫製や、一部のボトムスの縫製を行っているようです。
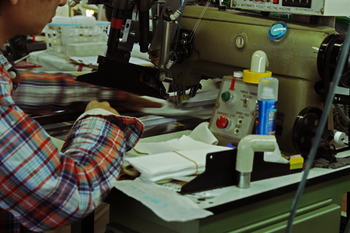
両玉縁ポケットをつくる特殊なミシン。若い職人さんがベテランの職人さんのアドバイスを受けながら、手早く動いていました。技術の継承が難しくなってきているというお話を聞きましたが、実際にやってみて長い年月をかけて身についていくものなんだと改めて実感します。
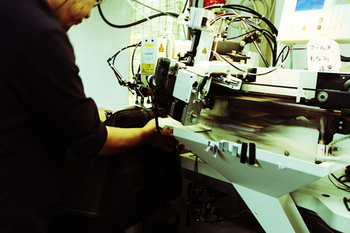
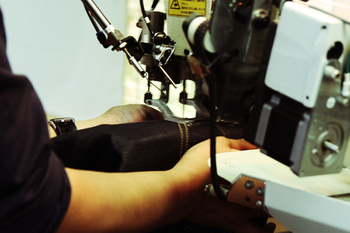
力強い手さばきが印象的です。ちなみにこちらがベルトループを作る特殊ミシンのようです。
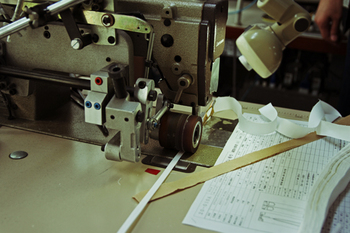
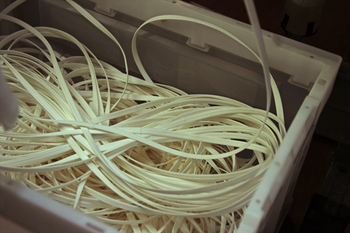
効率を重視し、国内から海外へその拠点を移していく企業が多い中で、地場での生産にこだわり、長年培われた技術の継承と新しい事への取り組みを地道に続けていく。こういう姿勢が根強いファンを生んでいるんですね。
二つの工場見学を後に、瀬戸大橋を渡り再び児島に戻ります。
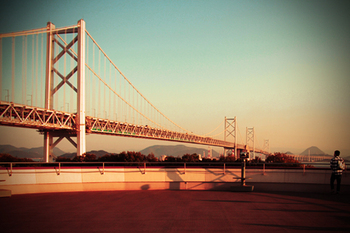
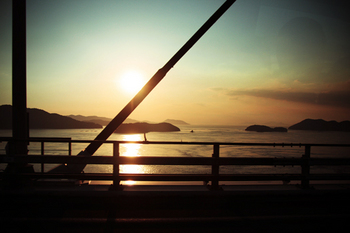
次はプライベートで撮影に来たいですね。
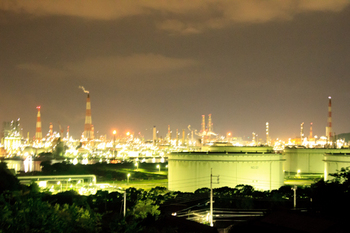
次回は、「加工」「染色」「素材」に関してのリポートをお届けします。
それでは。 Ryuichi Tsukada